The Growing Impact of **Injection Mold Makers** in Metal Fabrication
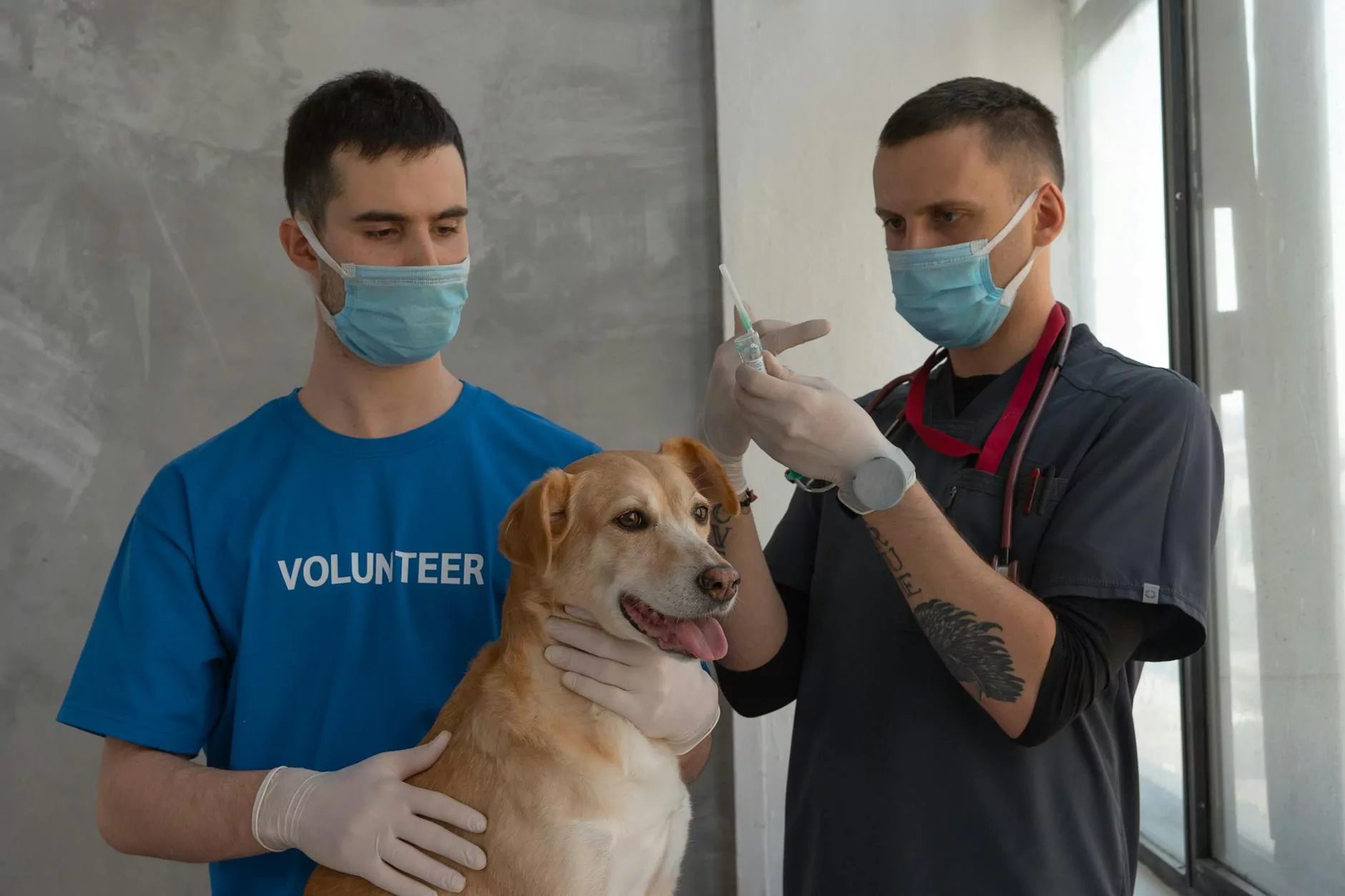
In today's highly competitive market, businesses are constantly seeking ways to enhance their production efficiency and quality. One essential aspect of this endeavor is injection mold makers, who play a critical role in the metal fabrication industry. This article will delve into the intricate world of injection molding, highlighting the pivotal contributions of injection mold makers and exploring how their expertise is shaping the future of manufacturing.
Understanding Injection Molding
Injection molding is a manufacturing process used to create parts by injecting molten material into a mold. This method is particularly popular for producing metal parts and components due to its ability to achieve high precision and intricate designs. The process involves several crucial stages:
- Material Selection: Choosing the right material is critical. Common materials include various plastics and metals, with the choice often dictated by the application's specific demands.
- Mold Design: This stage involves creating a mold that can withstand the pressure of injected material. The design must account for shrinkage, cooling time, and other factors that affect the final product.
- Injection Process: The molten material is injected into the mold under high pressure, allowing it to take the desired shape.
- Cooling and Ejection: Once the material solidifies, it is cooled down and ejected from the mold.
Benefits of Using Injection Molding in Metal Fabrication
Injection molding offers numerous advantages that make it a preferred choice in the metal fabrication sector:
- High Volume Production: Injection molding can produce large quantities of parts quickly, making it ideal for mass production.
- Precision and Consistency: Injection molds can create highly complex shapes with consistent dimensions, ensuring that every part meets stringent quality standards.
- Cost-Effectiveness: Although initial setup costs can be high, the per-part cost decreases significantly as production volume increases.
- Materials Versatility: A wide range of materials can be used in the injection molding process, allowing for varied applications across industries.
Role of Injection Mold Makers in Metal Fabrication
Injection mold makers are the artisans behind the efficient functioning of the injection molding process. Their expertise encompasses several key areas:
1. Mold Design and Engineering
The process begins with innovative design. Mold makers utilize advanced software to create 3D models of the mold. This stage involves:
- Prototyping: Developing prototypes to test the mold's functionality before final production.
- Design Optimization: Refining the design based on feedback and simulation results to ensure optimal performance.
2. Precision Machining
Once the design is finalized, the mold makers engage in precision machining. This step includes:
- Advanced Technologies: Utilizing CNC machines and other technology to create exact mold cavities.
- Quality Assurance: Maintaining rigorous standards throughout the machining process to avoid defects.
3. Testing and Validation
Before molds are deployed in production, they must undergo extensive testing:
- Trial Runs: Conducting initial runs to identify any issues in the mold and fine-tuning as necessary.
- Performance Evaluation: Analyzing the performance of the mold and ensuring it meets production requirements.
The Future of Injection Mold Making
The industry is witnessing rapid advancements that promise to enhance the capabilities of injection mold makers. Key trends include:
1. Automation and Robotics
Automation technologies are revolutionizing the injection molding process. Robots are increasingly used in tasks such as:
- Material Handling: Efficiently managing materials reduces the risk of contamination.
- Quality Control: Machines equipped with AI can conduct real-time monitoring to ensure quality compliance.
2. Sustainable Manufacturing Practices
As the manufacturing sector embraces sustainability, injection mold makers are exploring eco-friendly materials and processes:
- Recyclable Materials: Using materials that can be recycled and reprocessed.
- Energy-Efficient Machines: Investing in machinery that utilizes less energy during the molding process.
3. Advanced Materials
The development of new materials is opening doors to innovation in product design. Trends include:
- Composite Materials: Integrating different materials for enhanced performance and weight reduction.
- High-Temperature Plastics: Allowing for components that can withstand extreme operating conditions.
Choosing the Right Injection Mold Makers
When looking for top-notch injection mold makers, consider the following factors:
- Experience: Look for mold makers with a proven track record in the industry.
- Technology: Verify that they utilize state-of-the-art technology for mold design and production.
- Customization: Ensure they are capable of providing tailored solutions that meet your specific needs.
- Customer Support: A responsive support team can significantly enhance the partnership's value.
Conclusion
The role of injection mold makers is indispensable in the ever-evolving world of metal fabrication. Their skills not only contribute to the production of high-quality components but also drive innovation and efficiency in manufacturing processes. By embracing cutting-edge technologies and sustainable practices, injection mold makers are setting the stage for a more advanced and eco-friendly industry landscape.
In summary, as the demand for precision-engineered metal parts continues to grow, investing in the expertise of esteemed injection mold makers becomes increasingly vital for businesses aiming to thrive in today’s competitive market.