Understanding Die Casting: A Closer Look at Metal Fabrication
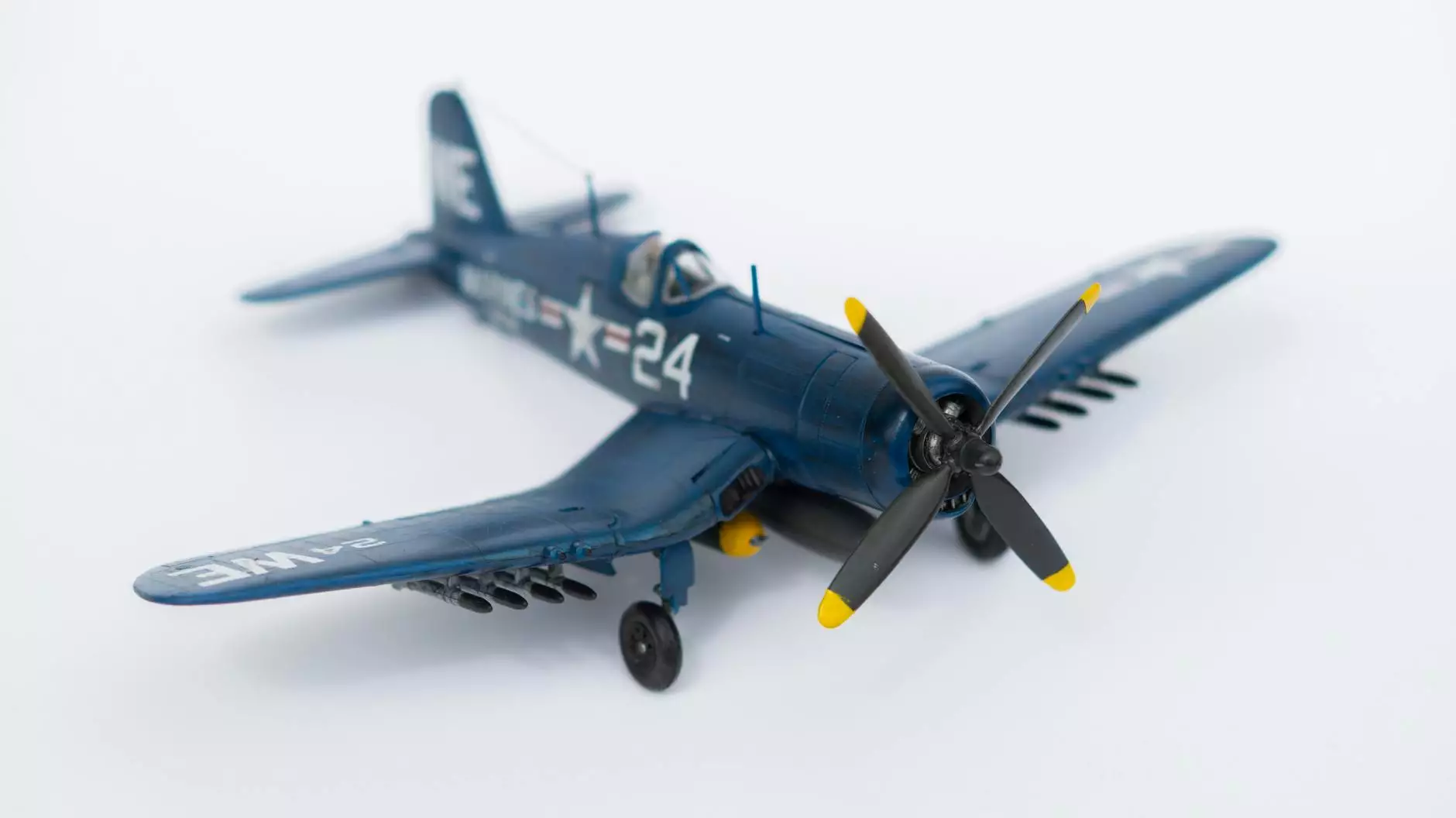
What is Die Casting?
Die casting is a manufacturing process that involves forcing molten metal into a mold cavity. This method is highly regarded in the field of metal fabrication for creating complex shapes with high precision. Die casting is commonly used with non-ferrous metals such as aluminum, zinc, and magnesium. The process is efficient, and when executed properly, it results in products with superior surface finish and dimensional accuracy.
How Die Casting Works
The die casting process consists of several key steps:
- Preparation: The mold, or die, must first be created. This is usually made from steel and is durable enough to withstand the high pressure generated during the casting process.
- Heating: The metal is heated to a specific temperature until it becomes molten.
- Injection: The molten metal is rapidly injected into the die through a nozzle under high pressure. This ensures that every crevice of the mold is filled.
- Cooling: After injection, the metal is allowed to cool and solidify within the mold.
- Removal: Once cooled, the die is opened, and the newly cast part is removed.
Advantages of Die Casting
Die casting offers numerous advantages, making it a preferred method in metal fabrication:
- Precision and Complexity: Die casting allows for the creation of intricate designs with precise dimensions.
- Surface Finish: Parts produced via die casting typically possess a smoother surface finish compared to other metalworking methods.
- High Production Rates: This process is suitable for mass production, significantly reducing manufacturing costs per unit.
- Material Efficiency: Minimal waste is produced due to the controlled process, making it an economical choice.
Common Applications of Die Casting
Die casting is widely used across various industries, including:
- Automotive Industry: Used for parts like engine blocks, transmission cases, and wheels.
- Aerospace: Components that demand high strength-to-weight ratios.
- Electronics: Cases for devices as well as internal components.
- Consumer Goods: Items such as household appliances and tools.
Choosing the Right Die Casting Manufacturer
When looking for a die casting manufacturer, consider the following factors to ensure quality and service excellence:
- Experience and Expertise: Look for manufacturers with a proven track record in die casting processes.
- Technology and Equipment: Ensure they use the latest technology and machinery for optimal results.
- Quality Management Systems: Reliable manufacturers implement stringent quality control processes.
- Customer Service: Opt for manufacturers that provide excellent support and clear communication throughout the production process.
The Future of Die Casting in Metal Fabrication
As technology evolves, so does the die casting industry. Innovations in materials and processes, such as 3D printing of molds, are paving the way for new possibilities in die casting. Sustainable practices, including reduced energy consumption and enhanced recycling processes, are becoming increasingly important.
Furthermore, the integration of smart technologies and automation is expected to revolutionize how die casting manufacturers operate, leading to even greater efficiency and precision.
Conclusion
In summary, partnering with a knowledgeable and skilled die casting manufacturer can significantly enhance the outcomes of your metal fabrication efforts. Understanding die casting's processes, advantages, and applications will enable your business to take full advantage of this effective manufacturing method.
Whether you're in the automotive, aerospace, or consumer goods industry, die casting offers a myriad of benefits that lead to high-quality products and streamlined production processes. Embrace this robust method to enhance your manufacturing capability and maintain a competitive edge in your respective market.
For more insights and services related to die casting, explore our offerings at deepmould.net.