Choosing the Best Die Casting Mold Supplier for Your Business
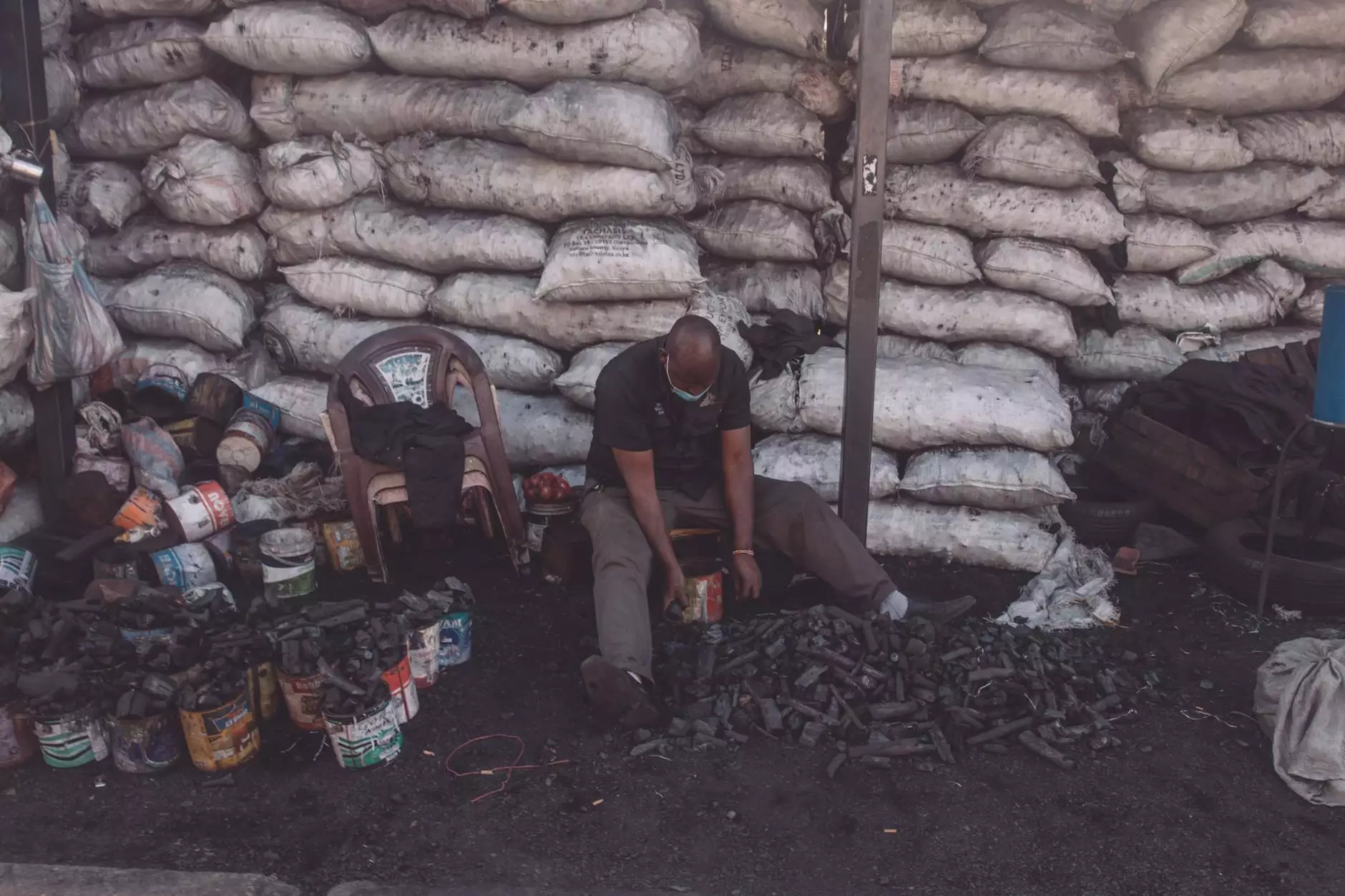
Die casting is an essential manufacturing process that involves forcing molten metal into a mold cavity. This technique is widely utilized across various industries, including automotive, aerospace, and consumer electronics. As a result, selecting the right die casting mold supplier is crucial for ensuring the quality, durability, and efficiency of your products.
Understanding Die Casting: The Basics
The die casting process allows manufacturers to produce complex shapes with high precision. The process primarily utilizes two types of metals: zinc and aluminum. Here’s a brief overview:
- Zinc Die Casting: Known for its high strength and resistance to corrosion, zinc die casting is often used in applications that require durability.
- Aluminum Die Casting: Light yet strong, aluminum castings are prevalent in the automotive and aerospace sectors due to their excellent thermal conductivity.
Why Partner with a Reputable Die Casting Mold Supplier?
Choosing a reliable die casting mold supplier can significantly impact your manufacturing success. Here are some critical benefits:
- Quality Assurance: A reputable supplier uses advanced technology and experienced technicians to ensure the molds meet the highest industry standards.
- Cost Efficiency: An experienced supplier optimizes the manufacturing process, reducing waste and minimizing costs, which translates to savings for your business.
- On-time Delivery: Reliable suppliers understand the value of time in manufacturing and provide timely deliveries to keep your production schedule on track.
- Custom Solutions: They can collaborate with you to create customized molds tailored to your specific product needs, enhancing your competitive edge.
Factors to Consider When Choosing a Die Casting Mold Supplier
When searching for a suitable die casting mold supplier, several factors should guide your decision:
1. Experience and Expertise
Evaluate the supplier’s experience in the industry. An established supplier is likely to have improved their processes over time, leading to higher quality products. Look specifically for:
- Years of operation in the die casting industry
- Portfolio of previous projects
- Client testimonials and case studies
2. Technology and Equipment
Modern technology plays a significant role in the quality of die casting molds. Ensure the supplier utilizes advanced machines and techniques such as:
- Computer Numerical Control (CNC) machining for precision
- 3D modeling and simulation software for design accuracy
- Quality control technologies, including injection pressure sensors and thermocouples
3. Material Selection
The choice of material for the molds is vital. Confirm that your supplier uses high-grade materials to ensure durability and longevity. Some commonly used materials include:
- Tool steel for strength
- Aluminum for lighter molds
- Copper alloys for excellent thermal conductivity
4. Communication and Customer Service
Effective communication is essential in any business relationship. A good supplier should be responsive and willing to answer your questions. Assess their customer service capabilities such as:
- Availability of a dedicated account manager
- Clarity in quoting and pricing structures
- Commitment to customer follow-ups post-project completion
How to Collaborate Effectively with Your Die Casting Mold Supplier
Establishing a productive partnership with your die casting mold supplier can lead to mutual success. Here are some best practices:
1. Clearly Define Your Requirements
Before engaging with a supplier, develop a thorough understanding of your product needs, including:
- Dimensions and tolerances
- Production volumes
- Lead times and delivery schedules
2. Engage in Open Dialogue
Maintain constant communication throughout the project. Encourage feedback from your supplier and be open to suggestions that could improve the final product quality.
3. Regularly Review Progress
Schedule regular meetings or progress reports to ensure everything is on track. This will help address any unforeseen issues quickly and maintain deadlines.
4. Celebrate Successes Together
Recognizing the hard work and achievements of your supplier fosters a positive relationship. When milestones are met, consider acknowledging the effort put into meeting your demands.
Case Studies: Successful Partnerships with Die Casting Mold Suppliers
To illustrate the importance of selecting the right die casting mold supplier, let's explore some successful partnerships:
Case Study 1: Automotive Component Supplier
A leading automotive manufacturer faced challenges with part defects, leading to increased costs. After switching to a specialized die casting mold supplier, they achieved:
- 20% reduction in production costs
- 30% increase in production efficiency
- Significant decrease in part rejection rates
Case Study 2: Consumer Electronics Brand
A consumer electronics brand required high-precision aluminum components for their new product line. By partnering with a specialized supplier, they benefited from:
- Faster turnaround times, enabling a quicker market launch
- Improved product quality, leading to enhanced customer satisfaction
- Lower overall manufacturing costs due to efficient processes
The Future of Die Casting and Its Impact on Suppliers
The die casting industry is continually evolving with advancements in technology, materials, and processes. The future will likely see:
- Increased Automation: Automating various stages of die casting can lead to higher production rates and lower labor costs.
- Sustainability Efforts: Suppliers are expected to adopt more environmentally friendly practices, such as recycling waste materials and using sustainable energy sources.
- Smart Manufacturing: Incorporating IoT and AI in die casting could enable real-time data analysis for improved decision-making and quality control.
Conclusion
Selecting the right die casting mold supplier is crucial for any business aiming to maintain a competitive edge in today’s fast-paced market. By considering factors such as experience, technology, and material selection, and by establishing a strong collaborative relationship, you can significantly enhance your manufacturing capabilities. Remember, the right partnership not only improves product quality but can also lead to substantial cost savings and operational efficiencies. Explore your options, do your research, and ensure you choose a supplier that aligns with your business goals. Your success in die casting begins with this essential decision.