Rubber Bellows Prototype: Revolutionizing Industrial Solutions
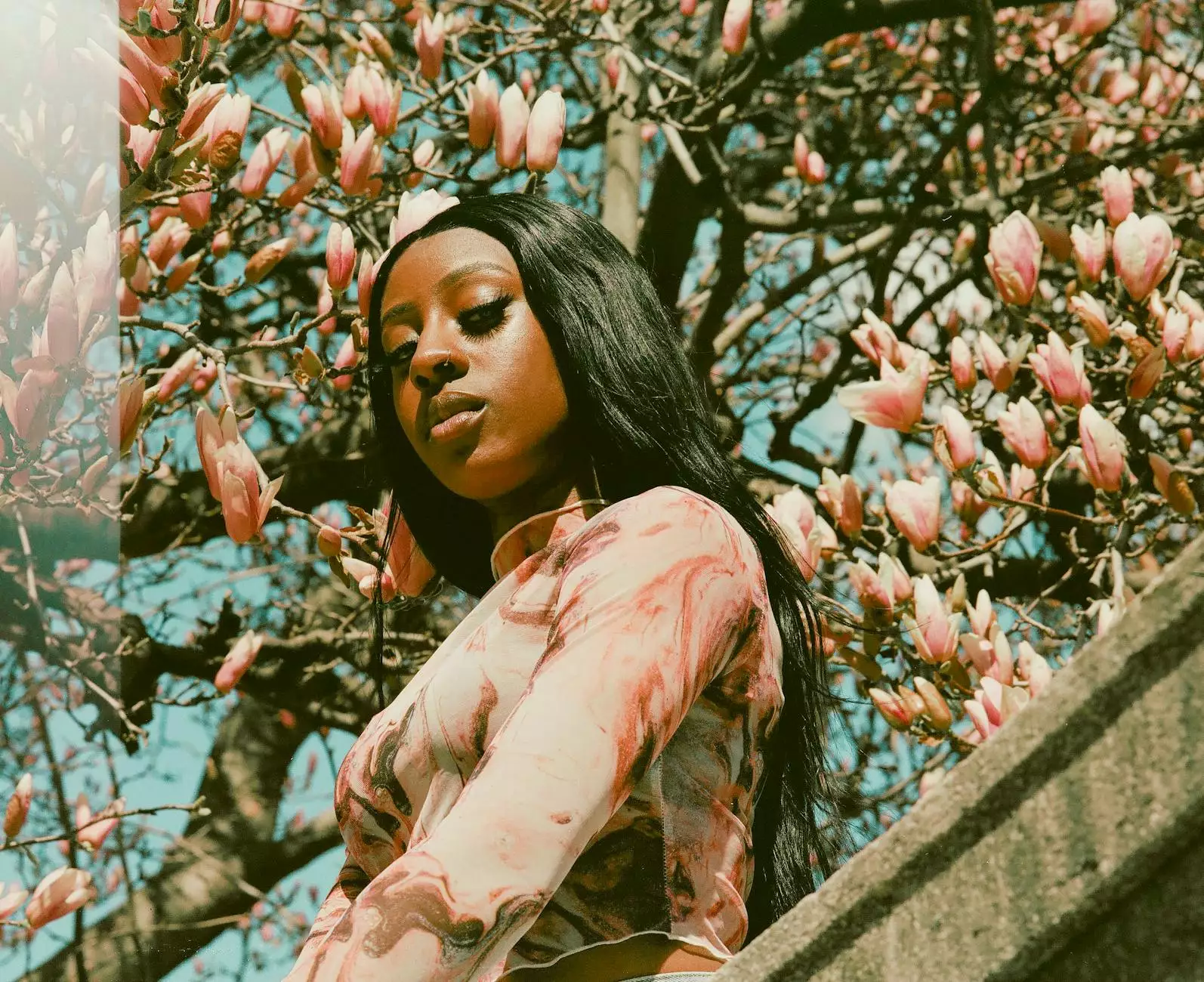
The industrial landscape has seen remarkable advancements in recent years, particularly in the realm of rubber bellows prototypes. These innovative components have become essential in numerous applications across various industries, providing durability, flexibility, and reliability. This article delves into the significance of rubber bellows prototypes, their applications, and how OVictor Group stands at the forefront of this technological evolution with their superior 3D printing capabilities.
Understanding Rubber Bellows
Rubber bellows are flexible containers or enclosures designed to protect sensitive components from dust, dirt, and moisture while allowing for relative motion between parts. They are widely used in various sectors, including automotive, aerospace, medical, and manufacturing.
What Are Rubber Bellows?
Rubber bellows are typically made from elastomeric materials that provide excellent flexibility and an ability to withstand various environmental conditions. Their primary purpose is to safeguard moving parts and mechanisms, absorbing vibrations and accommodating misalignments.
Key Characteristics of Rubber Bellows
- Flexibility: Rubber bellows can stretch and compress, making them ideal for applications that involve motion.
- Durt Resistance: They effectively protect components from dirt and contaminants.
- Water Resistance: Rubber materials offer excellent water resistance, essential for outdoor and industrial applications.
- Temperature Tolerance: They can withstand a wide range of temperatures, ensuring performance in diverse environments.
Applications of Rubber Bellows Prototypes
The versatility of rubber bellows prototypes allows them to be applied in many different fields. Here are some notable applications:
1. Automotive Industry
In the automotive sector, rubber bellows are utilized in shock absorbers, steering columns, and more. They protect delicate parts of vehicles while ensuring smooth operation under varying conditions.
2. Aerospace
Aerospace applications require components that can function efficiently in extremely harsh conditions. Rubber bellows are used to protect sensitive actuators and sensors in aircraft, where reliability is paramount.
3. Medical Devices
The medical industry relies heavily on components that are not only durable but also hygienic. Rubber bellows in medical devices ensure the protection of sensitive mechanisms while complying with health regulations.
4. Manufacturing and Robotics
In manufacturing and robotic applications, rubber bellows are found in machinery where they protect moving parts from debris while allowing for precision movement and control.
The Role of Prototyping in Developing Rubber Bellows
Prototyping plays a critical role in the successful creation of rubber bellows. It allows designers to visualize and test their concepts before final production, ensuring functionality and performance.
Benefits of Prototyping Rubber Bellows
- Validation of Design: Prototypes allow for testing of the design under real-world conditions.
- Cost-Effectiveness: Identifying design flaws early can save money in the long run by avoiding costly production errors.
- Customization: Prototyping provides the opportunity to customize designs based on specific client needs and applications.
OVictor Group’s Innovation in Rubber Bellows Prototyping
At OVictor Group, we leverage advanced 3D printing technology to provide innovative solutions in rubber bellows prototyping. Our cutting-edge manufacturing processes ensure high-quality prototypes that meet the rigorous demands of various industries.
Why Choose OVictor Group?
- Expertise: Our team of engineers and designers specializes in creating custom rubber bellows prototypes tailored to client specifications.
- Advanced Technology: Utilizing the latest 3D printing techniques leads to accurate and efficient productions.
- Sustainability: Our processes emphasize recycling and efficient material usage, contributing to eco-friendly practices.
Our Prototyping Process
- Consultation: We work closely with clients to understand their specific needs and requirements.
- Design: Our team creates detailed designs based on client input and industry standards.
- Prototyping: We produce prototypes using advanced 3D printing technologies, allowing for rapid iterations.
- Testing: Each prototype is rigorously tested to ensure it meets all performance specifications.
- Production: Upon approval, we move forward with large-scale production of the rubber bellows.
The Future of Rubber Bellows Prototypes
As industries continue to evolve, the need for reliable, high-quality rubber bellows prototypes will increase. With ongoing advancements in 3D printing and material science, we can expect even greater performance and durability from these crucial components.
Innovations on the Horizon
Emerging technologies and materials are set to transform the landscape of rubber bellows manufacturing. Anticipated trends include:
- Smart Materials: The integration of sensors into rubber bellows for real-time monitoring.
- Enhanced Customization: More economical and efficient customization options thanks to 3D printing advancements.
- Biodegradable Materials: Sustainable options that minimize environmental impact during end-of-life disposal.
Conclusion
The significance of rubber bellows prototypes in today’s industrial environment cannot be overstated. Their versatility and durability make them indispensable across various sectors. OVictor Group stands poised to lead this charge with our innovative 3D printing capabilities, providing tailored solutions that meet the ever-changing demands of our customers.
As we look to the future, our commitment to quality and sustainability will guide our efforts in revolutionizing the way rubber bellows are designed and manufactured. By partnering with OVictor Group, businesses can ensure they are equipped with the best solutions available, whether in automotive, aerospace, medical, or manufacturing industries.